Right. I guess that this is part two of my DIY acrylic scales thread. At the time I was too tired to write what essentially is a subject of its own. So here it is. Hold onto your hats. 
There is no point spending time cutting and sanding your own scales if you have no way of attaching them to your blade. There are micro screws and fasteners available which you do up like tiny nuts and bolts. They work, but to my eye look untidy and are, well, basically cheating, IMO. The reason why you have gone to so much trouble making custom scales in the first place is because you want the job done right. You might as well see the thing through.
As covered in the DIY scales thread, the first thing to do is drill the holes. You will be wanting some sort of fixed drill press for this. It does not need to be big or powerful but it needs to be fixed so that those holes go in straight, especially for the pivot pin. I use a 1/16 drill bit as this seems the right diameter for the hole in most blades, and that size rod, which we will be making the pins from, is common and easy to get hold of.
The pins themselves are just short cut lengths of bar stock. You can buy it in brass or nickel silver. They both work well but the brass is cheaper and easier to get. You'll find it in most model and hobby stores. It is usually only costs a couple of bucks per foot, enough to make LOTS of pins.
Put the rod in the hole to gauge the length and cut it off with snips. You can buy flush cutters that do a neater job, but normal wire cutters work. The problem with them is that they leave a pinched end that you will need to tidy up.
That's in part two...

There is no point spending time cutting and sanding your own scales if you have no way of attaching them to your blade. There are micro screws and fasteners available which you do up like tiny nuts and bolts. They work, but to my eye look untidy and are, well, basically cheating, IMO. The reason why you have gone to so much trouble making custom scales in the first place is because you want the job done right. You might as well see the thing through.
As covered in the DIY scales thread, the first thing to do is drill the holes. You will be wanting some sort of fixed drill press for this. It does not need to be big or powerful but it needs to be fixed so that those holes go in straight, especially for the pivot pin. I use a 1/16 drill bit as this seems the right diameter for the hole in most blades, and that size rod, which we will be making the pins from, is common and easy to get hold of.
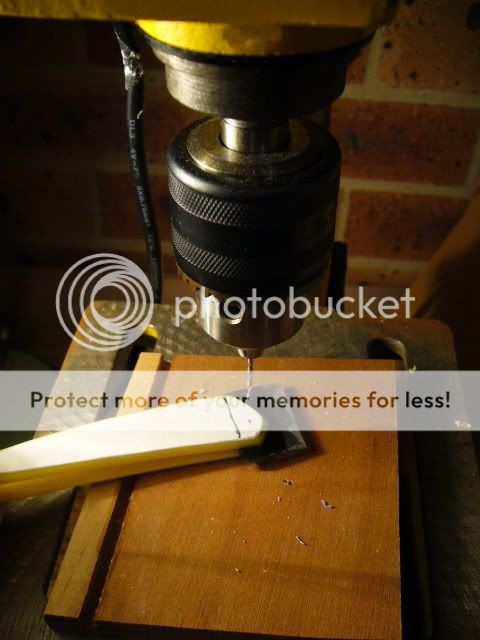
The pins themselves are just short cut lengths of bar stock. You can buy it in brass or nickel silver. They both work well but the brass is cheaper and easier to get. You'll find it in most model and hobby stores. It is usually only costs a couple of bucks per foot, enough to make LOTS of pins.
Put the rod in the hole to gauge the length and cut it off with snips. You can buy flush cutters that do a neater job, but normal wire cutters work. The problem with them is that they leave a pinched end that you will need to tidy up.
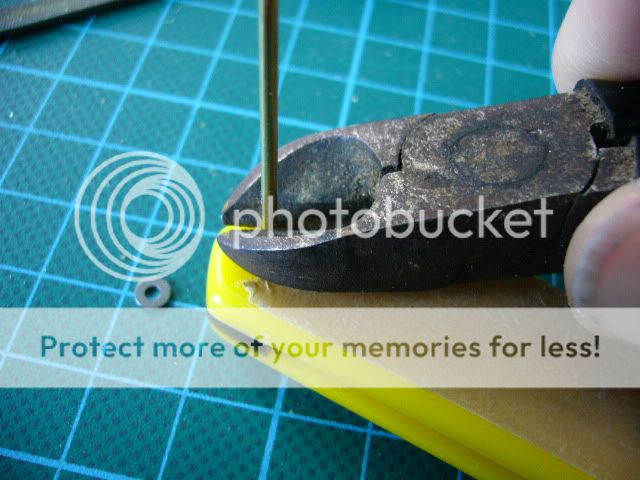
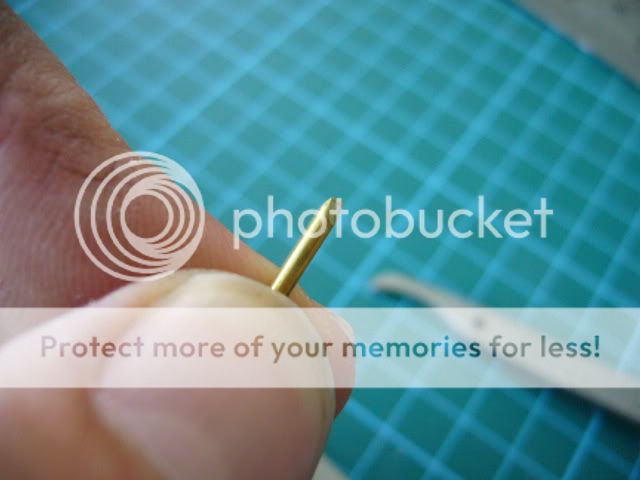
That's in part two...
Last edited: