I had this all typed out once, but like the unorganized oaf I am, I deleted it. Several of you asked how to do it, I know a couple who told me with success. So to contribute, and to remove the mystery, here is my method.
THREE PIN STRAIGHTENING with heat!!
You will need:
A vise (4" is a good size. larger is good for knives, but not necessary for razors.)
A propane torch, there are hotter gases available, but we wont be dealing with high temp.
Some 3/16 to 1/4 brass rod - 3 pieces, I bend them in a "L" shape so they hang better on the vise.
And I will get you to fashion a high volume spray bottle. So get a bottle, a 1 liter pop bottle works great. Drill 10 - 20 holes 1/16" in diameter in the lid, a basic nozzle.
You will also need some room temperature water, and a bucket to catch falling water.
So you have a blade knife or razor, that has a bend in it.., Bloody Gremlins messin' with you again!
Oh yeah, I forgot, you will also need a firm constitution! (or balls! lol)
Step 1, you have likely done. Figure where the bend is, and which direction.
Step 2, you will need to place the brass pins and the blade in the vise, and snug things up to hold firmly. I will now refer to the bend with the terms convex side, and concave side.
So you will need 2 pins on the concave side, one either side of the bend, the other pin goes on the convex side, center of the bend. And as I said, snug them up only!
Step 3, Depending on the severity of the bend, the following may need to be repeated several times in small steps, with practice your, ummm, constitution will grow in size, and you may be more willing to take risks. Now, apply some pressure to the blade by tightening the vise a tad, you will need to watch as the blade begins to bend. A longer blade will show the flex more than a short razor. if you are comfortable stop! I take no responsibility for snapped blades!!
Step 4, Get the water bottle ready, and position the catch basin under the vice.
Step 5, Time to turn up the heat!! So fire up the torch, moderate flame. Here is the theory... Heat relaxes steel, it will also temper steel, and if heated to cherry red and cooled slowly, will anneal, or remove all hardness from steel. Water is good and bad. Water on a warm blade will cool it. Water on a hot blade will shock it. Water on a very hot blade (critical heat) will quench it. If done incorrectly, the blade will let you know with the dreaded "tink" sound... You just cracked the blade.... So sorry, you constitution just acorned! Lol!! We WILL NOT be getting any where near those temps!
So the process... With your built in timer, you will keep count of seconds, or at the very least, even intervals that resemble seconds. You are going to apply heat to the blade, waving the flame from side to side, with the water bottle at the ready ( near the vise) Count off 12 seconds, then immediately douse the blade with a large volume of water. release the tension on the vise, and check to see if the bend is gone, improved, or didn't change at all.
If the bend is corrected, congratulations!! Go have a beer! If it has improved, good. Tighten the vise again, apply a little more pressure, reheat for the same time as before, and douse, then check. Continue till straight. If there is no change. Re-tighten to the same amount as before, re-heat, but add two or three seconds. Douse with water, and check again. Continue to increase time under heat, each subsequent cycle, until the desired level of "straight" is achieved ( some people will be happy with an improvement, that prevents scale rubbing, other anal few, like my self, won't be happy with out true alignment. You may have to counter bend the blade before the desired amount of set is achieved. On a shallow bend, sometimes the first heat will be done on a blade whos bend will be counterbent.
WORDS OF CAUTION!
Cold is safe, hot is not! We are playing in the middle. By heating/relaxing the steel, then cooling/setting/shocking the steel, we are trying to freeze movement where we want it. That being where the blade is straight. Now Heat can ruin a temper. Usually on simple steels back in the day, temper was drawn by color. Straw to blue/purple. Each color is achieved at different temperatures.
Simple carbon steels temper between 300 and 450 degrees depending on the target hardness. That color is light straw, and getting up to brown and blues is a sign the temper has been altered negatively. So as long as our treatment is done watching and controlling what we do by watching the color change, we have a level of safety for our project. So if you see straw colors, you are reaching your go-no go point. Any more you run the risk of altering the temper. proceed, if necessary, with caution... Or stop. Your call.
AN EXPLANATION OF HEAT AND COLORS
If steel has been freshly ground, sanded, or polished, it will form an oxide layer on its surface when heated. As the temperature of the steel is increased, the thickness of the iron oxide will also increase. Although iron oxide is not normally transparent, such thin layers do allow light to pass through, reflecting off both the upper and lower surfaces of the layer. This causes a phenomenon called thin-film interference, which produces colors on the surface. As the thickness of this layer increases with temperature, it causes the colors to change from a very light yellow, to brown, then purple, then blue. These colors appear at very precise temperatures, and provide the blacksmith with a very accurate gauge for measuring the temperature. The various colors, their corresponding temperatures, and some of their uses are:
Faint-yellow – 176 °C (349 °F) – engravers, razors, scrapers
Light-straw – 205 °C (401 °F) – rock drills, reamers, metal-cutting saws
Dark-straw – 226 °C (439 °F) – scribers, planer blades
Brown – 260 °C (500 °F) – taps, dies, drill bits, hammers, cold chisels
Purple – 282 °C (540 °F) – surgical tools, punches, stone carving tools
Dark blue – 310 °C (590 °F) – screwdrivers, wrenches
Light blue – 337 °C (639 °F) – springs, wood-cutting saws
Grey-blue – 371 °C (700 °F) and higher – structural steel
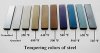
[FONT=&]Beyond the grey-blue color, the iron oxide loses its transparency, and the temperature can no longer be judged in this way. The layer will also increase in thickness as time passes, which is another reason overheating and immediate cooling is used. Steel in a tempering oven, held at 205 °C (401 °F) for a long time, will begin to turn brown, purple or blue, even though the temperature did not exceed that needed to produce a light-straw color. Oxidizing or carburizing heat sources may also affect the final result. The iron oxide layer, unlike rust, also protects the steel from corrosion through passivation.[/FONT]
Some modern smelts of steels, have tempering temperatures nearing or exceeding 1000F degrees. CPM M4 for example hardens at 2130F degrees and tempers at 1050F. So in all reality, you are doing no damage until you reach the temperature at which the steel was tempered.
EXAPMLE STEEL - 1095
Below, see a table for a steel called 1095. This is a steel still used today in modern razors, and I suspect very near in composition to razor steel of old. This steel is a high carbon steel, and is a good example to dispel myths about temperature. I will touch on all facets of working this steel.
Recommended Working Sequence For 1095
Forging: heat to 2100°F (1150°C) . Do not forge below 1500°F (815°C).
Normalizing: Heat to 1575°F (855°C). Cool in still air.
Annealing: Heat to 1475°F (800°C). Furnace cool to 1200°F (650°C) at a rate not exceeding 50°F (28°C) per hour.
Grinding or Machining
Hardening: Austenitize- Heat to 1475°F (800°C). Can be quenched in water or brine with care but can also be oil quenched in sections under 1/4 in. (6.35 mm) thick
Tempering: As-quenched hardness of approximately 66 HRC. Hardness can be adjusted downward by proper tempering.
So as you can see, you have to hit 450-500 degrees on a carbon blade to alter the hardness by 1 point.
USING A HEAT SINK
There are commercial pastes available that are used as heat sinks doing soldering work, for example silver soldering guards on hunting knives. The do work, no question. I don't use them when I straighten blades. An even heating is more important, and in my mind superior to localized heating. We are already manipulating stress in the steel. Why add more?
Also, there has been talk of keeping the blade super cool while working/buffing it, this is safe, but not entirely necessary. If its too hot to touch/hold, by all means cool it. You can safely work it hot, if you can hold it, don't worry about it. If you see no color change, you are fine. If you see tan/straw color, your ok, but this is the limit.
I hope this helps any of the adventurous among us.
EDIT:
For those of you with out a shop, or tools such as a vice, you can do the same work with simple tools. A couple c clamps, vise grips, 4 inch nail, an piece of plywood, 2 X 4, flat bar, or angle iron.
So to set up, I will use flat bar as my example. Position a C clamp, plyers or vise grips around the flat bar, leaving room for the tang of the razor. Position the razor, with the convex part of the bend towards the bar, tighten until it makes contact with the tang. Now slide a brass rod, 4" nail, piece of dowel whatever you have, between the razor and the bar at the high point of the bend. Place the other clamp around the bar and razor near the tip of the razor, and snug it up. this will tighten the hold on the tang as well. Carefully apply pressure by tightening the clamp until you see the bend change. The use the same procedures as above.
I use this method quite often with long lazy bends on knives where a 4" vise is to narrow to do the repair I need to do. So I'm not just tossing bogus info at you. I do this stuff a lot. It works. And is way safer then just slipping a pipe around it and forcing the bend cold. I'm sure there have been a few snapped blades doing it that way.
For those who have had bends on the edge, this method will work there as well. Reduce the duration of the heat cycles, and pay close attention to any color change. I will say again. It will take a minimum of 300 degrees to adversely affect temper. Remember that a proper tempering cycle has the blade held at 300 to 500 degrees for HOURS to evenly temper the blade to a desired hardness.
Use the same technique, but maybe smaller pins to achieve the bends required to correct. Again I do this on 300 mm blades with a ripple on the edge. IT WORKS FINE!! Tested hardness values were minute to no change.
Paranoia, folk lore, and superstition, are evil bed mates!
THREE PIN STRAIGHTENING with heat!!
You will need:
A vise (4" is a good size. larger is good for knives, but not necessary for razors.)
A propane torch, there are hotter gases available, but we wont be dealing with high temp.
Some 3/16 to 1/4 brass rod - 3 pieces, I bend them in a "L" shape so they hang better on the vise.
And I will get you to fashion a high volume spray bottle. So get a bottle, a 1 liter pop bottle works great. Drill 10 - 20 holes 1/16" in diameter in the lid, a basic nozzle.
You will also need some room temperature water, and a bucket to catch falling water.
So you have a blade knife or razor, that has a bend in it.., Bloody Gremlins messin' with you again!
Oh yeah, I forgot, you will also need a firm constitution! (or balls! lol)
Step 1, you have likely done. Figure where the bend is, and which direction.
Step 2, you will need to place the brass pins and the blade in the vise, and snug things up to hold firmly. I will now refer to the bend with the terms convex side, and concave side.
So you will need 2 pins on the concave side, one either side of the bend, the other pin goes on the convex side, center of the bend. And as I said, snug them up only!
Step 3, Depending on the severity of the bend, the following may need to be repeated several times in small steps, with practice your, ummm, constitution will grow in size, and you may be more willing to take risks. Now, apply some pressure to the blade by tightening the vise a tad, you will need to watch as the blade begins to bend. A longer blade will show the flex more than a short razor. if you are comfortable stop! I take no responsibility for snapped blades!!
Step 4, Get the water bottle ready, and position the catch basin under the vice.
Step 5, Time to turn up the heat!! So fire up the torch, moderate flame. Here is the theory... Heat relaxes steel, it will also temper steel, and if heated to cherry red and cooled slowly, will anneal, or remove all hardness from steel. Water is good and bad. Water on a warm blade will cool it. Water on a hot blade will shock it. Water on a very hot blade (critical heat) will quench it. If done incorrectly, the blade will let you know with the dreaded "tink" sound... You just cracked the blade.... So sorry, you constitution just acorned! Lol!! We WILL NOT be getting any where near those temps!
So the process... With your built in timer, you will keep count of seconds, or at the very least, even intervals that resemble seconds. You are going to apply heat to the blade, waving the flame from side to side, with the water bottle at the ready ( near the vise) Count off 12 seconds, then immediately douse the blade with a large volume of water. release the tension on the vise, and check to see if the bend is gone, improved, or didn't change at all.
If the bend is corrected, congratulations!! Go have a beer! If it has improved, good. Tighten the vise again, apply a little more pressure, reheat for the same time as before, and douse, then check. Continue till straight. If there is no change. Re-tighten to the same amount as before, re-heat, but add two or three seconds. Douse with water, and check again. Continue to increase time under heat, each subsequent cycle, until the desired level of "straight" is achieved ( some people will be happy with an improvement, that prevents scale rubbing, other anal few, like my self, won't be happy with out true alignment. You may have to counter bend the blade before the desired amount of set is achieved. On a shallow bend, sometimes the first heat will be done on a blade whos bend will be counterbent.
WORDS OF CAUTION!
Cold is safe, hot is not! We are playing in the middle. By heating/relaxing the steel, then cooling/setting/shocking the steel, we are trying to freeze movement where we want it. That being where the blade is straight. Now Heat can ruin a temper. Usually on simple steels back in the day, temper was drawn by color. Straw to blue/purple. Each color is achieved at different temperatures.
Simple carbon steels temper between 300 and 450 degrees depending on the target hardness. That color is light straw, and getting up to brown and blues is a sign the temper has been altered negatively. So as long as our treatment is done watching and controlling what we do by watching the color change, we have a level of safety for our project. So if you see straw colors, you are reaching your go-no go point. Any more you run the risk of altering the temper. proceed, if necessary, with caution... Or stop. Your call.
AN EXPLANATION OF HEAT AND COLORS
If steel has been freshly ground, sanded, or polished, it will form an oxide layer on its surface when heated. As the temperature of the steel is increased, the thickness of the iron oxide will also increase. Although iron oxide is not normally transparent, such thin layers do allow light to pass through, reflecting off both the upper and lower surfaces of the layer. This causes a phenomenon called thin-film interference, which produces colors on the surface. As the thickness of this layer increases with temperature, it causes the colors to change from a very light yellow, to brown, then purple, then blue. These colors appear at very precise temperatures, and provide the blacksmith with a very accurate gauge for measuring the temperature. The various colors, their corresponding temperatures, and some of their uses are:
Faint-yellow – 176 °C (349 °F) – engravers, razors, scrapers
Light-straw – 205 °C (401 °F) – rock drills, reamers, metal-cutting saws
Dark-straw – 226 °C (439 °F) – scribers, planer blades
Brown – 260 °C (500 °F) – taps, dies, drill bits, hammers, cold chisels
Purple – 282 °C (540 °F) – surgical tools, punches, stone carving tools
Dark blue – 310 °C (590 °F) – screwdrivers, wrenches
Light blue – 337 °C (639 °F) – springs, wood-cutting saws
Grey-blue – 371 °C (700 °F) and higher – structural steel
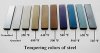
[FONT=&]Beyond the grey-blue color, the iron oxide loses its transparency, and the temperature can no longer be judged in this way. The layer will also increase in thickness as time passes, which is another reason overheating and immediate cooling is used. Steel in a tempering oven, held at 205 °C (401 °F) for a long time, will begin to turn brown, purple or blue, even though the temperature did not exceed that needed to produce a light-straw color. Oxidizing or carburizing heat sources may also affect the final result. The iron oxide layer, unlike rust, also protects the steel from corrosion through passivation.[/FONT]
Some modern smelts of steels, have tempering temperatures nearing or exceeding 1000F degrees. CPM M4 for example hardens at 2130F degrees and tempers at 1050F. So in all reality, you are doing no damage until you reach the temperature at which the steel was tempered.
EXAPMLE STEEL - 1095
Below, see a table for a steel called 1095. This is a steel still used today in modern razors, and I suspect very near in composition to razor steel of old. This steel is a high carbon steel, and is a good example to dispel myths about temperature. I will touch on all facets of working this steel.
Recommended Working Sequence For 1095
Forging: heat to 2100°F (1150°C) . Do not forge below 1500°F (815°C).
Normalizing: Heat to 1575°F (855°C). Cool in still air.
Annealing: Heat to 1475°F (800°C). Furnace cool to 1200°F (650°C) at a rate not exceeding 50°F (28°C) per hour.
Grinding or Machining
Hardening: Austenitize- Heat to 1475°F (800°C). Can be quenched in water or brine with care but can also be oil quenched in sections under 1/4 in. (6.35 mm) thick
Tempering: As-quenched hardness of approximately 66 HRC. Hardness can be adjusted downward by proper tempering.
Tempering Temperature | Rockwell Hardness | ||
[SUP]o[/SUP]C | [SUP]o[/SUP]F | HRC | |
149 | 300 | 65 | |
177 | 350 | 63-64 | |
204 | 400 | 62-63 | |
232 | 450 | 61-62 | |
260 | 500 | 59-60 | |
288 | 550 | 57-58 | |
316 | 600 | 55-56 | |
343 | 650 | 53-54 |
So as you can see, you have to hit 450-500 degrees on a carbon blade to alter the hardness by 1 point.
USING A HEAT SINK
There are commercial pastes available that are used as heat sinks doing soldering work, for example silver soldering guards on hunting knives. The do work, no question. I don't use them when I straighten blades. An even heating is more important, and in my mind superior to localized heating. We are already manipulating stress in the steel. Why add more?
Also, there has been talk of keeping the blade super cool while working/buffing it, this is safe, but not entirely necessary. If its too hot to touch/hold, by all means cool it. You can safely work it hot, if you can hold it, don't worry about it. If you see no color change, you are fine. If you see tan/straw color, your ok, but this is the limit.
I hope this helps any of the adventurous among us.
EDIT:
For those of you with out a shop, or tools such as a vice, you can do the same work with simple tools. A couple c clamps, vise grips, 4 inch nail, an piece of plywood, 2 X 4, flat bar, or angle iron.
So to set up, I will use flat bar as my example. Position a C clamp, plyers or vise grips around the flat bar, leaving room for the tang of the razor. Position the razor, with the convex part of the bend towards the bar, tighten until it makes contact with the tang. Now slide a brass rod, 4" nail, piece of dowel whatever you have, between the razor and the bar at the high point of the bend. Place the other clamp around the bar and razor near the tip of the razor, and snug it up. this will tighten the hold on the tang as well. Carefully apply pressure by tightening the clamp until you see the bend change. The use the same procedures as above.
I use this method quite often with long lazy bends on knives where a 4" vise is to narrow to do the repair I need to do. So I'm not just tossing bogus info at you. I do this stuff a lot. It works. And is way safer then just slipping a pipe around it and forcing the bend cold. I'm sure there have been a few snapped blades doing it that way.
For those who have had bends on the edge, this method will work there as well. Reduce the duration of the heat cycles, and pay close attention to any color change. I will say again. It will take a minimum of 300 degrees to adversely affect temper. Remember that a proper tempering cycle has the blade held at 300 to 500 degrees for HOURS to evenly temper the blade to a desired hardness.
Use the same technique, but maybe smaller pins to achieve the bends required to correct. Again I do this on 300 mm blades with a ripple on the edge. IT WORKS FINE!! Tested hardness values were minute to no change.
Paranoia, folk lore, and superstition, are evil bed mates!
Last edited: