Hi again,
Because I botched my first restoration posting (taking a phone call while I was writing and uploading pictures) I thought I would start over and try again. I'll also split this post up and build it up with replies.
So here goes.
I bought six straights for about $70 and they were all from 1945 or there about. I don't know when they were made, but that was when they were bought - new. They were pretty beaten up and 4 or 5 will need new scales, pins, etc.
To start on this project I had to get a workshop up and running in my shed. This is what I've bought:
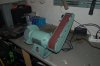
First item, a cheap $45 belt / wheel grinder. This item is a godsend for working on the scales. Brilliant! I don't use the stone wheel, just the belt grinder.
next:
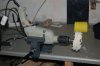
I had an old drill - so together with a vice, I built a wheel polisher. Again, a must and this time a very cheap way of doing it.
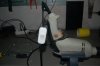
I installed an on/off switch on the power cable and clamped the drill power button down. I can adjust the speed of the drill by tightening or loosening the the band around the power button.
On the end of the drill is a spindle tap for mounting the cloth polishing wheels.
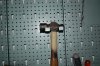
I found this old ball pane hammer for $1 at a junk sale that I'll use for the pinning.
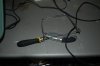
I bought a stanley coping saw from a regular hardware store. This turned out to be a disappointment. When I made my first set of acrylic scales I just cut two strips of black, opaque acrylic plexi-glass and stuck them together with double sided tape.
I did not need the coping saw (which was really awkward to use) because the belt grinder is fantastic for getting the basic scale shape out of the acrylic strips.
More to come in a moment ...
Because I botched my first restoration posting (taking a phone call while I was writing and uploading pictures) I thought I would start over and try again. I'll also split this post up and build it up with replies.
So here goes.
I bought six straights for about $70 and they were all from 1945 or there about. I don't know when they were made, but that was when they were bought - new. They were pretty beaten up and 4 or 5 will need new scales, pins, etc.
To start on this project I had to get a workshop up and running in my shed. This is what I've bought:
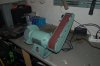
First item, a cheap $45 belt / wheel grinder. This item is a godsend for working on the scales. Brilliant! I don't use the stone wheel, just the belt grinder.
next:
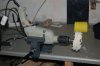
I had an old drill - so together with a vice, I built a wheel polisher. Again, a must and this time a very cheap way of doing it.
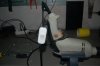
I installed an on/off switch on the power cable and clamped the drill power button down. I can adjust the speed of the drill by tightening or loosening the the band around the power button.
On the end of the drill is a spindle tap for mounting the cloth polishing wheels.
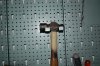
I found this old ball pane hammer for $1 at a junk sale that I'll use for the pinning.
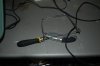
I bought a stanley coping saw from a regular hardware store. This turned out to be a disappointment. When I made my first set of acrylic scales I just cut two strips of black, opaque acrylic plexi-glass and stuck them together with double sided tape.
I did not need the coping saw (which was really awkward to use) because the belt grinder is fantastic for getting the basic scale shape out of the acrylic strips.
More to come in a moment ...